Diaphragm walls are rigid reinforced concrete walls made up a number of discrete panels joined together to form a single continuous wall. The rectangular shape of a diaphragm wall is well suited to resist bending and shear forces associated with lateral soil loads which makes them efficient for deeper excavations.
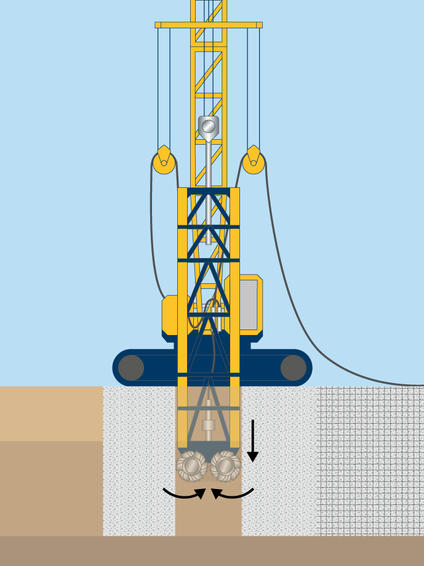
Common uses
Process
Diaphragm walls can be constructed in widths ranging between 450mm and 1500mm and to depths up to 100m+. The techniques used to construct the panels provide tight joint tolerances ensuring high quality structural connection between the panels and very low permeability. Diaphragm walls are ideal for lateral earth support for deep excavations as well as forming a cut off wall, and are often incorporated as the permanent building basement walls. This can create project savings by eliminating the need for temporary earth support and dewatering. These walls can be designed and construction with integral waler beams and anchor block outs reducing the time and complexity of the excavation process.
For a structural diaphragm wall, the temporary support slurry is replaced with concrete and some type of reinforcement for resisting structural loads. For a non structural slurry wall, the specially designed temporary support slurry is left in place to self harden or replaced with plastic (or low strength) concrete.
Diaphragm walls are constructed under a support fluid usually a Bentonite slurry or polymer, and are excavated using rope clam shell grabs, hydraulic clam shell grabs or hydromill cutters or combination of all three. The choice of system is dependant on the geology/hydrology and depth and purpose of wall required. An individual panel plan is developed specifically for each project, determining the length of each panel based on trench stability assessments. The panel may have a plan shaped as Xs, Ts or Ys to suit specific project requirements and the joints will be designed as stop ends or overcuts, to suit the methodology adopted. Stop ends are steel shutters that are placed at the ends of panel to cast the panel up against and can incorporate a water bar. When the adjacent panel is excavated these are removed.
The alternative when using a hydromill is to overcut the previous panel to form a keyed joint between two panels. Once the excavation of the panel is complete and the cleaning process completed the reinforcement cage is placed and the panel concrete placed by tremie. The displaced support fluid is sent back to the fluid plant for cleaning ready for re-use.
Advantages
Quality assurance
Keller has a fleet of specialist wall excavation and construction equipment to complete all types of diaphragm wall and load bearing elements (also known as a ‘barrette’). Keller's experience in this technique ensures that the important pre-commencement planning and panel layout and production sequencing are untaken in collaboration with the client ensuring the most efficient process is guaranteed. All functions of the trenching are monitored real time and recorded in line with Keller’s processes and procedures which are independently assessed as being compliant to FSC and Australian standards ISO 9001 & ISO 14001.